Tecno Logica stands out for its ability to design and create completely customized automation solutions for the industrial sector, responding to the most complex and specific production needs. Our multi-sector experience allows us to intervene in different production contexts, developing customized systems where there are no standard solutions or "ready to buy" products on the market.
Our applications
From busbar production to radiator processing, up to more specific industrial applications, we approach each project with an advanced engineering approach, combining technology, efficiency and maximum integration into existing processes. Furthermore, our transversal know-how allows us to draw on technologies, ideas and solutions developed in other sectors, adapting them to the specific context with an innovative vision.
We design custom systems tailored to every need.
Thanks to the modularity and flexibility of our solutions, we optimize every stage of the production process—improving performance, reducing cycle times, and ensuring a fast return on investment. Regardless of the industry, our goal is to deliver systems that transform industrial production, enhance competitiveness, and meet technological challenges with innovative, high-performance solutions.
Automatic or semi-automatic system represents an example of efficiency and precision in the production of busbars, ensuring quality and reliability at every stage of the process:
- Wrapping the bars with Mylar: The system automatically wraps the bars with Mylar, ensuring perfect insulation and long-lasting protection against electrical and mechanical stress.
- Bending the bars: The system bends the bars according to the required specifications, ensuring that each curve is performed with maximum accuracy for an optimal fit.
- Composition of the busbar bundle: The system assembles the bars into neat bundles, ready for installation.
- Housing of the busbar bundles: The busbar bundles are housed inside the cases, which keep them firm and protected, ready to play their role in the electrical systems.
- Electrical test: Carrying out the electrical acceptance tests.
- Palletization: possibility of palletizing the busbar bundles, preparing them for transport.
Possibility of processing busbars batch 1.
Busbar wrapping with Mylar
Automatic insulation of Mylar wrapped busbars ensuring uniform coverage without gaps and improving insulation performance. After wrapping, the bars are automatically inspected to ensure the reliability and safety of the final product.
Busbar Bending
The process of bending busbars is crucial to adapting them to electrical system configurations. It begins with measuring and marking the bending point, followed by securing the busbar in a bending machine. Bending is performed using a constant force, monitoring the angle to ensure accuracy. After bending, the busbar is inspected for accuracy.
Busbar bundle composition
The system automatically assembles the bars into strapped bundles through the following steps:
Pack placement: The bars are collected in bundles and placed on a roller or belt conveyor, ready for strapping.
Pack securing: The automatic strapping machine securely locks the bundle of bars, ensuring that it remains stable during the strapping process2.
Strap application: The machine wraps a polypropylene, polyester or metal strap around the bundle of bars. The strap is then tensioned to ensure a secure binding.
Sealing: The strap is sealed by welding or stapling, depending on the material used. This ensures that the binding remains intact during transport.
Quality control: After strapping, the bundle is inspected to ensure that the binding is correct and secure.
Benefits: Automatic strapping increases efficiency, reduces processing times and improves transport safety, minimising the risk of damage to the bars.
Housing of busbar bundles
The automated housing of busbar bundles is conducted automatically in-line using manipulators and/or robots to ensure accuracy, efficiency and safety.
Here is a detailed description of the process:
Initial placement: The busbar bundles are placed on an automatic conveyor that takes them to the housing station.
Alignment and securing: A machine vision and sensor system accurately aligns the busbar bundles. Robots/manipulators secure the bundles in place to prevent movement during housing.
Insertion into housing: Robots/manipulators pick up the pre-formed housings and position them around the busbar bundles. This may include the use of clips, screws or other securing mechanisms to ensure the housing is secure.
Sealing and insulation: The housing is sealed to protect the busbars from moisture, dust and other contaminants. Insulating materials are applied to ensure electrical safety.
Electrical Test
Quality control: Sensors and electrical test systems inspect the housing to ensure that it has been applied correctly and that there are no defects.
Labelling and traceability: Each housing is labelled with traceability information to facilitate future handling and maintenance.
Palettizing
Palletizing robots/manipulators are programmed to pick up and place products on pallets precisely and quickly. These robots can handle a wide range of automotive components, from small parts to large and heavy components.
Discover Tecno Logica’s solutions
Automatic or semi-automatic system represents an example of efficiency and precision in the production of busbars, ensuring quality and reliability at every stage of the process:
- Wrapping the bars with Mylar: The system automatically wraps the bars with Mylar, ensuring perfect insulation and long-lasting protection against electrical and mechanical stress.
- Bending the bars: The system bends the bars according to the required specifications, ensuring that each curve is performed with maximum accuracy for an optimal fit.
- Composition of the busbar bundle: The system assembles the bars into neat bundles, ready for installation.
- Housing of the busbar bundles: The busbar bundles are housed inside the cases, which keep them firm and protected, ready to play their role in the electrical systems.
- Electrical test: Carrying out the electrical acceptance tests.
- Palletization: possibility of palletizing the busbar bundles, preparing them for transport.
Possibility of processing busbars batch 1.
Busbar wrapping with Mylar
Automatic insulation of Mylar wrapped busbars ensuring uniform coverage without gaps and improving insulation performance. After wrapping, the bars are automatically inspected to ensure the reliability and safety of the final product.
Busbar Bending
The process of bending busbars is crucial to adapting them to electrical system configurations. It begins with measuring and marking the bending point, followed by securing the busbar in a bending machine. Bending is performed using a constant force, monitoring the angle to ensure accuracy. After bending, the busbar is inspected for accuracy.
Busbar bundle composition
The system automatically assembles the bars into strapped bundles through the following steps:
Pack placement: The bars are collected in bundles and placed on a roller or belt conveyor, ready for strapping.
Pack securing: The automatic strapping machine securely locks the bundle of bars, ensuring that it remains stable during the strapping process2.
Strap application: The machine wraps a polypropylene, polyester or metal strap around the bundle of bars. The strap is then tensioned to ensure a secure binding.
Sealing: The strap is sealed by welding or stapling, depending on the material used. This ensures that the binding remains intact during transport.
Quality control: After strapping, the bundle is inspected to ensure that the binding is correct and secure.
Benefits: Automatic strapping increases efficiency, reduces processing times and improves transport safety, minimising the risk of damage to the bars.
Housing of busbar bundles
The automated housing of busbar bundles is conducted automatically in-line using manipulators and/or robots to ensure accuracy, efficiency and safety.
Here is a detailed description of the process:
Initial placement: The busbar bundles are placed on an automatic conveyor that takes them to the housing station.
Alignment and securing: A machine vision and sensor system accurately aligns the busbar bundles. Robots/manipulators secure the bundles in place to prevent movement during housing.
Insertion into housing: Robots/manipulators pick up the pre-formed housings and position them around the busbar bundles. This may include the use of clips, screws or other securing mechanisms to ensure the housing is secure.
Sealing and insulation: The housing is sealed to protect the busbars from moisture, dust and other contaminants. Insulating materials are applied to ensure electrical safety.
Electrical Test
Quality control: Sensors and electrical test systems inspect the housing to ensure that it has been applied correctly and that there are no defects.
Labelling and traceability: Each housing is labelled with traceability information to facilitate future handling and maintenance.
Palettizing
Palletizing robots/manipulators are programmed to pick up and place products on pallets precisely and quickly. These robots can handle a wide range of automotive components, from small parts to large and heavy components.
Discover Tecno Logica’s solutions
Systems designed to efficiently assemble radiators using both automatic and semi-automatic processes. Includes the following main functions:
Tube Cutting
- Automatic Tube Cutting Machines: These machines cut tubes precisely to the required lengths using advanced cutting technologies. The process is fully automated, ensuring high accuracy and consistency.
- Semi-Automatic Tube Cutting Stations: Operators assist in feeding tubes into cutting machines, which then perform the cutting operation. This allows flexibility in handling different tube sizes and materials.
Welding
- Automatic Welding Robots: These robots perform high-precision welding of tubes and other components. They are programmed to follow specific welding patterns, ensuring strong and reliable joints.
- Semi-Automatic Welding Stations: Skilled operators handle welding torches and perform welding manually, with the assistance of jigs and fixtures to ensure accuracy.
Final acceptance tests
- Automated Test Systems: These systems perform various tests on the assembled radiators, such as pressure tests, leak tests and performance tests. The results are recorded and analyzed to ensure that each radiator meets quality standards.
- Manual Test Stations: Operators perform additional tests and inspections, using specialized tools and equipment to verify the quality and functionality of the radiators.
Tube Cutting
CNC cutting systems for aluminum bars capable of performing complex cuts on different profiles with high precision and repeatability.
Welding
Robotic cells to perform welding and assembly efficiently. These cells can be configured to perform different operations, such as welding frames and other structural parts through MIG/MAG, spot or laser welding.
Testing
Palletizing robots/manipulators are programmed to pick up and place products onto pallets precisely and quickly. These robots can handle a wide range of components, from small parts to larger and heavier components.
Systems designed to efficiently assemble radiators using both automatic and semi-automatic processes. Includes the following main functions:
Tube Cutting
- Automatic Tube Cutting Machines: These machines cut tubes precisely to the required lengths using advanced cutting technologies. The process is fully automated, ensuring high accuracy and consistency.
- Semi-Automatic Tube Cutting Stations: Operators assist in feeding tubes into cutting machines, which then perform the cutting operation. This allows flexibility in handling different tube sizes and materials.
Welding
- Automatic Welding Robots: These robots perform high-precision welding of tubes and other components. They are programmed to follow specific welding patterns, ensuring strong and reliable joints.
- Semi-Automatic Welding Stations: Skilled operators handle welding torches and perform welding manually, with the assistance of jigs and fixtures to ensure accuracy.
Final acceptance tests
- Automated Test Systems: These systems perform various tests on the assembled radiators, such as pressure tests, leak tests and performance tests. The results are recorded and analyzed to ensure that each radiator meets quality standards.
- Manual Test Stations: Operators perform additional tests and inspections, using specialized tools and equipment to verify the quality and functionality of the radiators.
Tube Cutting
CNC cutting systems for aluminum bars capable of performing complex cuts on different profiles with high precision and repeatability.
Welding
Robotic cells to perform welding and assembly efficiently. These cells can be configured to perform different operations, such as welding frames and other structural parts through MIG/MAG, spot or laser welding.
Testing
Palletizing robots/manipulators are programmed to pick up and place products onto pallets precisely and quickly. These robots can handle a wide range of components, from small parts to larger and heavier components.
Discover Tecno Logica’s solutions
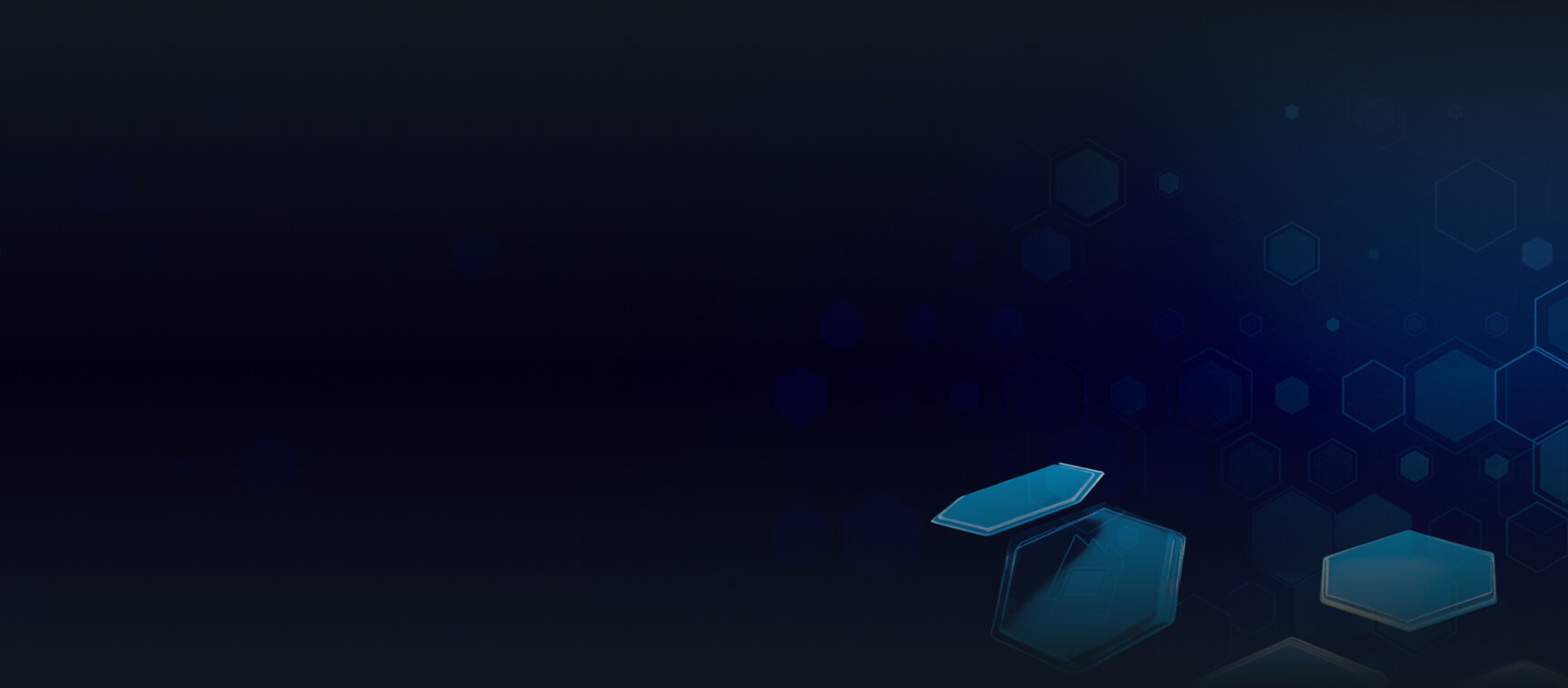
We are ready to listen, analyze and build tailor-made solutions for you.
Fill out the form below and one of our experts will contact you as soon as possible.